在选择齿轮淬火方式时,超高频淬火和中频淬火各有其独特的优势和适用场景。为了做出明智的选择,应综合考虑以下几个关键因素:
一、齿轮的尺寸与厚度
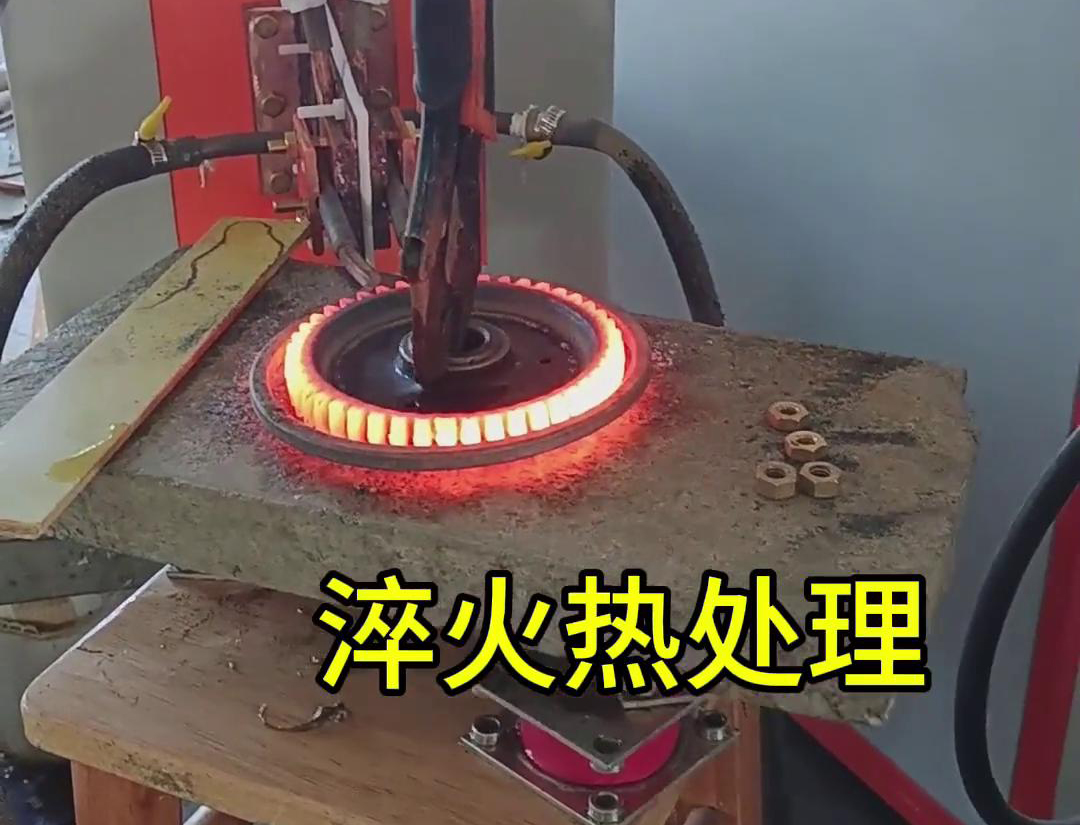
二、淬火层深度要求
- 超高频淬火:适用于较浅的淬火层深。超高频的特性决定了它在齿轮表面能够产生集中的热量,使得淬火层主要集中在表面附近。这种浅淬火层对于一些只需要表面高硬度、耐磨性好,而内部保持一定韧性的齿轮非常适用。
- 中频淬火:适用于较深的淬火层深。中频产生的磁场能够使热量深入齿轮内部,形成较深的淬火层。这对于一些需要有足够深的淬火层来承受巨大压力和剪切力的齿轮应用场景(如矿山机械、船舶推进系统中的齿轮)更为合适。
三、淬火时间与加热速度
- 超高频淬火:加热速度极快,能够在几秒甚至更短的时间内将齿轮表面加热到淬火温度。这对于一些对淬火时间有严格限制的生产流程非常有利。
- 中频淬火:相对来说加热速度稍慢,但能够在相对较长的时间内使齿轮整体温度升高。这样在淬火冷却后,齿轮从表面到内部的硬度变化相对较为平缓。
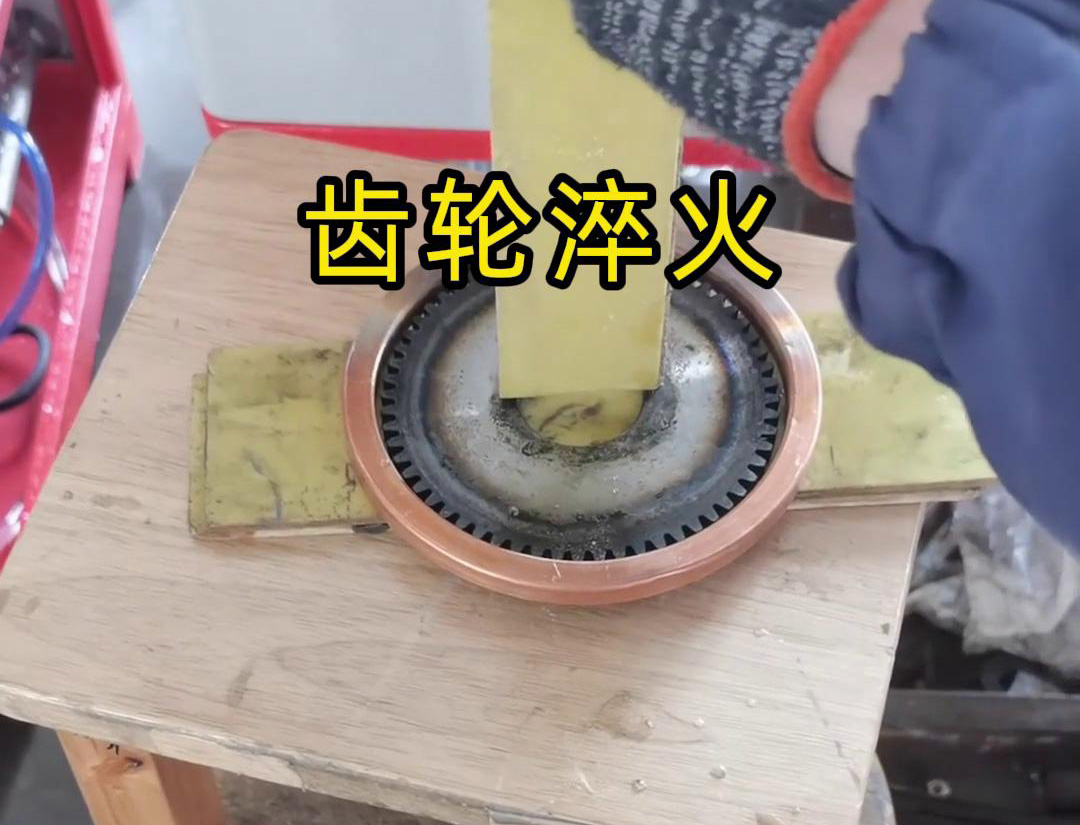
四、最终硬度与性能要求
- 超高频淬火:淬火后的齿轮表面硬度通常较高,这是因为快速加热使得齿轮表面的奥氏体化过程迅速完成,随后的淬火冷却能够形成细小、均匀的马氏体组织。这种高硬度表面对于抵抗齿轮表面的磨损和胶合等失效形式具有显著的效果。
- 中频淬火:在需要保持一定硬度梯度以平衡耐磨性和韧性的情况下是更好的选择。它能够在整个齿轮截面上保持一定的硬度分布,避免表面硬度极高而内部硬度骤降的情况。
五、生产成本与效率
- 超高频淬火:设备成本可能相对较高,但由于加热速度快,可以显著提高生产效率,适合大批量生产或需要快速淬火处理的场景。
- 中频淬火:设备成本相对较低,适用于各种规模的生产。虽然加热速度稍慢,但在保证淬火质量的前提下,仍然能够满足大多数齿轮的生产需求。
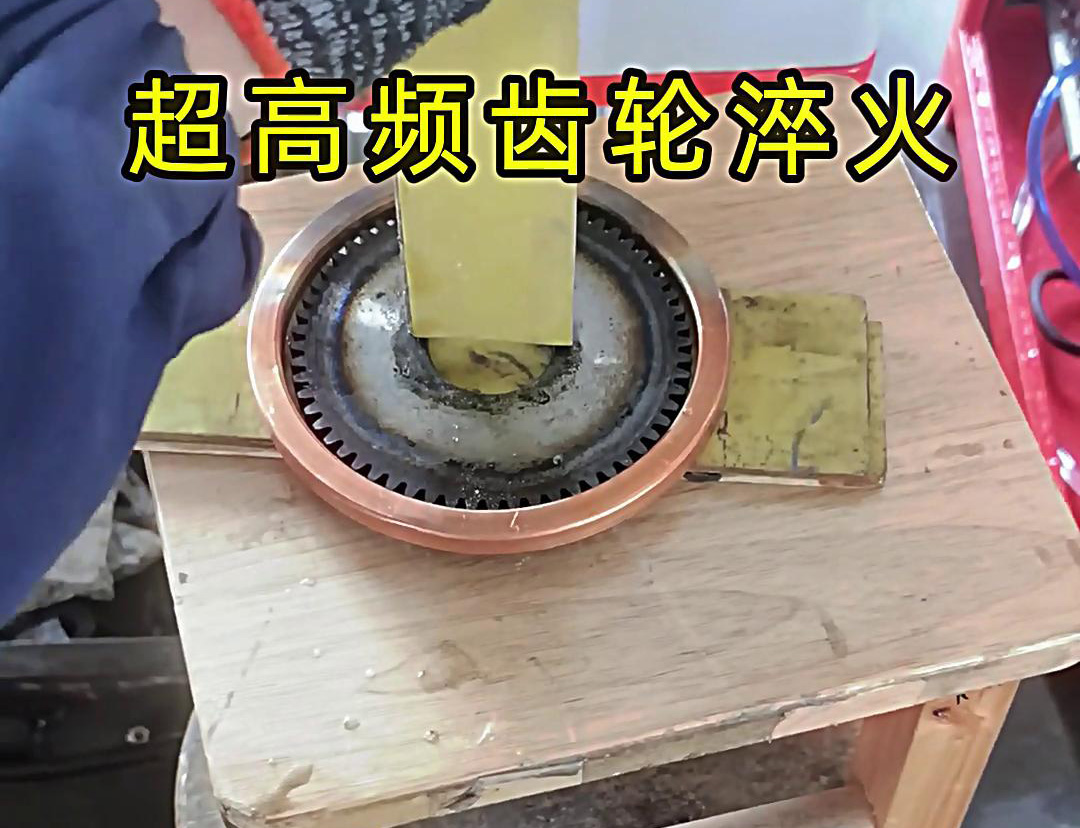
综上所述,在选择齿轮淬火方式时,应综合考虑齿轮的尺寸与厚度、淬火层深度要求、淬火时间与加热速度、最终硬度与性能要求以及生产成本与效率等因素。通过全面评估这些因素,可以做出最适合自己生产需求的淬火方式选择。
|